Kepler
10 MW
Decided for no real good reason that I needed a new road bike. Not being one to do things by half, I went out and purchased a new Trek Project One Domane SLR7 disc. Arrives in a month from the US as Project One bikes are custom assembled to the purchasers specification.
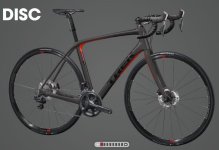
This meant I needed to sell current Trek 2015 Domane 5.9. to help fund this new purchase. Now this is nice bike and was looking for a very reasonable $3,000. Not a bite. Dropped it to $2,500. Still not a bite. No way was I going to let a bike like this with the latest Ultegra DI2 go for such a ridiculous price, so it got me thinking, can I convert this bike to use my friction drive and then sell off my current friction drive road bike as a complete package.
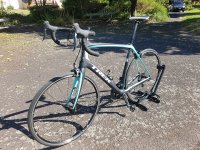
I had a bit of down time while I wait for the new locking plates to come back from the laser cutters so I decided to see if I could come up with a mount to suit the Trek's ultra wide BB90 bottom bracket.
The drive side bearing on a BB90 protrudes out from the bottom bracket but it does give you a bit of surface area to clamp too. Also with the bearing pressed into bottom bracket, it gave the clamping area quite a bit of crush strength.
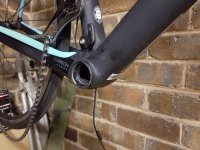
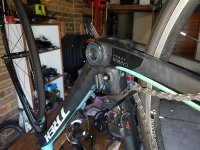
i also wanted to keep most of the standard drive mechanic parts and modify as little of drive design as little as possible. Turned out better then I had hoped with the mounting position being very rigid plus the added bonus of being easily adjustable.
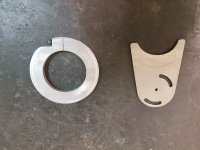
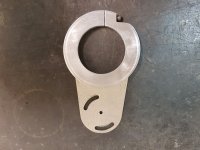
View attachment 3
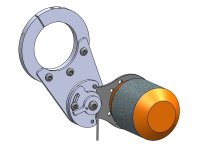
I am really pumped about converting this bike to use my friction drive. The bike was originally custom fitted to me and is such a comfortable ride. This bike will become my daily commuter with the new bike being my weekend bike.
Could this be the first ebike fitted with an Ultegra DI2 groupset.
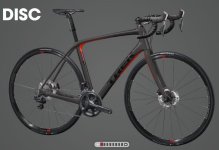
This meant I needed to sell current Trek 2015 Domane 5.9. to help fund this new purchase. Now this is nice bike and was looking for a very reasonable $3,000. Not a bite. Dropped it to $2,500. Still not a bite. No way was I going to let a bike like this with the latest Ultegra DI2 go for such a ridiculous price, so it got me thinking, can I convert this bike to use my friction drive and then sell off my current friction drive road bike as a complete package.
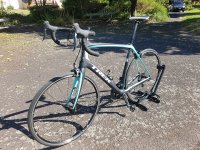
I had a bit of down time while I wait for the new locking plates to come back from the laser cutters so I decided to see if I could come up with a mount to suit the Trek's ultra wide BB90 bottom bracket.
The drive side bearing on a BB90 protrudes out from the bottom bracket but it does give you a bit of surface area to clamp too. Also with the bearing pressed into bottom bracket, it gave the clamping area quite a bit of crush strength.
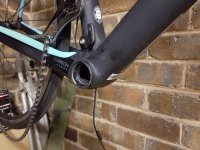
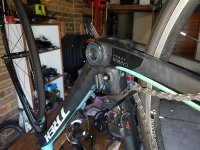
i also wanted to keep most of the standard drive mechanic parts and modify as little of drive design as little as possible. Turned out better then I had hoped with the mounting position being very rigid plus the added bonus of being easily adjustable.
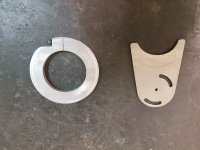
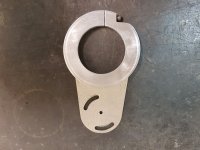
View attachment 3
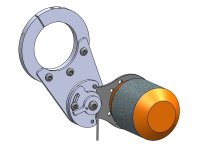
I am really pumped about converting this bike to use my friction drive. The bike was originally custom fitted to me and is such a comfortable ride. This bike will become my daily commuter with the new bike being my weekend bike.
Could this be the first ebike fitted with an Ultegra DI2 groupset.