AndyH said:
BMI said:
The fact is this project would not of gone ahead if the batteries were not available with minimum 5 years factory warranty.
What other manufacturer of LiFePO4 batteries are you aware of who is willing to provide 5 years warranty?
The packs will be housed in sealed custom made carbon fibre boxes to prevent salt water corrosion.
I would be happy to take photos to show you what they look like after 6 months in a marine environment.
It's my understanding that warranty can be any length one chooses and is more about the insurance policy than the product. People also think that bank deposit insurance is there to protect the consumer when it's really designed as a marketing tool used to increase cash flow for the bank.
Sorry Armin - I don't want to get off track. The question wasn't about the cell or the warranty or your ability to craft a battery. It was a question about how one ensures that all the connections stay tight over the life of the pack.
Just off the top of my head, I suppose one could safety-wire bolt heads, use a thread lock, or possibly use RTV on bolt heads. I'm from an aerospace background rather than marine, so my 'mind's eye' view of a sealed battery box has machined flanges, o-rings, over-pressure vents, and sealed pass-thru terminals. Not much overkill, there, probably...
We're looking out for you, Armin. We don't want to read about a boat fire caused by loose connections.
Andy, I am well aware of the Prius fire report which you attached. I have seen similar pack fires with A123 and other spot welded cells several times. In my professional opinion this is a major downfall of spot welded packs which use hundreds or even thousands of small cells like A123 cells.
I spoke with a local importer of electric wheel chair batteries made by PHET and there was a high failure rate of the cell joins breaking after only months of use due to metal fatigue in their LiFePO4 packs.
Since you are from an aerospace background you will be well aware of metal fatigue (I myself am from an aviation background and am a licenced pilot).
It is the repeated minor bumps, and jolting which a battery pack is subjected to thousands (or hundreds of thousands of times) which eventually results to cell weld link failures and possible fires. This minor movement within the pack as it is subjected to vibration by riding/driving on rough roads, pot holes etc. all causes slow but certain metal fatigue at the spot welded joints which may not show up for several years but there is a definite liklihood of cells failing at the spot welded joints at some time.
This is not a problem in a battery used in an electric drill for instance but for an electric vehicle application subjected to constant vibration it is a definite consideration.
I believe the threaded cell terminal design is much more reliable. Although it is possible for a cell link to come loose I have never seen this happen to date under normal use. The lock washer and precision torquing of the bolt seems to be adequate in actual practice. Of course this will be monitored as time goes on and as you mention for critical applications bolts could be lock wired as they are in aircraft.
Regarding warranty.....
Warranty has everything to do with reliability of the product and shows confidence the manufacturer believes their product will perform as they claim. If it didn't they would soon go out of business.
The warranty for my electric boat project is not something which I have just made up to satisfy the customer but is a fully factory backed warranty.
Warranty is all about the product (reliability) and nothing to do with insurance. If a product fails repeatedly due to lack of quality it won't be long before an insurance company won't insure you and you will go out of business.
I am sure that when LiFeTech confirmed the 5 year warranty for my boat customer they are confident there will be no problems. After all this is backed up by extensive testing of our cells and completed battery packs in the factory so I would think the factory engineers would have a pretty good idea of the reliability of our batteries when subjected to different forces.
LiFeTech has spent milliions of dollars on sophisticated cell and battery pack testing equipment so we can thoroughly test all our products and know they will perform as claimed.
Below are just a few photos showing various aspects of cell and battery pack testing at the LiFeTech factory. Individual cells are all tested and you can see from the pics that the completed packs are also tested. These pics show vibration testing of a complete pack so as to simulate different conditions in real life (such as driving on rough roads for example).
Yes, these photos are all taken at our LiFeTech factory and not at PSI or some other factory as others might claim.
View attachment 5
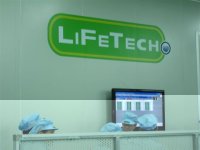