spinningmagnets
100 TW
I'm looking forward to retirement, because then I would have had the time to perform dozens of experiments that have been on the back burner for a couple years. Making a sandwich of copper/nickel is affordable and easily done with existing supply-line materials. DIY nickel-plated copper? what thickness of nickel is best? Maybe nickel-plated aluminum? Stainless plated aluminum? Anodized aluminum? Brass-plated aluminum/copper?
I was immediately reminded about a shill who posted a while back, and even though he only posted one of his companies products, it was worth knowing about, called SigmaCLAD. (original ES post here, https://endless-sphere.com/forums/viewtopic.php?f=14&t=68005&start=700 )
https://chargedevs.com/features/eng...lad-metal-experience-to-the-battery-industry/
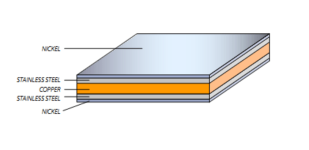
I was intrigued by the addition of a layer of stainless steel, which has an IACS conductivity rating of 3/100, compared to nickel at 23/100. Of course that makes it an excellent choice to easily spot-weld, but even as thin as its cross section would be, I think its a bad idea for ebike packs due to the horrible amount of resistance. And if you do add stainless, why add an additional layer of nickel? You can't always trust what manufacturers claim about their products, but we can still sometimes learn something valuable that might apply to us.
My first reaction was, why not just have nickel-clad copper? (cladding is a dry-process of bonding by rolling pressure, rather than electro-plating with chemicals). Wouldn't a three-layer material be cheaper to make than a five-layer material? The company PR release answered that question by saying the high conductivity of the copper core "overwhelmed" the spot-welding process. Of course, their customers may have demanded a material with no split, which would have forced the current direction through the cell-tip, rather than side-stepping through the bus itself.
I do believe it is possible for the cladding process to make bus material cheaper than electro-plating. They also mention that the symmetry of the clad materials helps it retain its shape when it heats up. If there were only two layers, the copper might expand from heat faster than the nickel, causing a pressure for the strip to bend. That being said, our goal is to allow a DIY battery pack that does not get hot when providing 15A-20A peaks per cell.
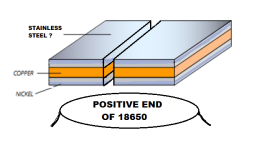
Is thin stainless cheaper than pure nickel and readily available locally in major cities? (doesn't need to be ordered). The lower layer would NEED to be nickel instead of stainless, because its conductivity is 23/3 better (7 times?) than stainless. If someone here got stuck with an order of nickel-plated steel ribbon (after they ordered pure nickel ribbon) then, the Ni-plated steel would likely be fine for the top cap...
I'm even now wondering if yellow brass would be acceptable for the lower layer. Its conductivity is less than copper (so it is more weldable with existing DIY machines), but conducts better than nickel...28/100, compared to 23/100... Brass is soft enough to be cut by scissors, and it is cheaper than Nickel.
I was immediately reminded about a shill who posted a while back, and even though he only posted one of his companies products, it was worth knowing about, called SigmaCLAD. (original ES post here, https://endless-sphere.com/forums/viewtopic.php?f=14&t=68005&start=700 )
https://chargedevs.com/features/eng...lad-metal-experience-to-the-battery-industry/
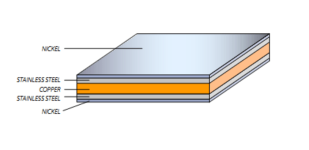
I was intrigued by the addition of a layer of stainless steel, which has an IACS conductivity rating of 3/100, compared to nickel at 23/100. Of course that makes it an excellent choice to easily spot-weld, but even as thin as its cross section would be, I think its a bad idea for ebike packs due to the horrible amount of resistance. And if you do add stainless, why add an additional layer of nickel? You can't always trust what manufacturers claim about their products, but we can still sometimes learn something valuable that might apply to us.
My first reaction was, why not just have nickel-clad copper? (cladding is a dry-process of bonding by rolling pressure, rather than electro-plating with chemicals). Wouldn't a three-layer material be cheaper to make than a five-layer material? The company PR release answered that question by saying the high conductivity of the copper core "overwhelmed" the spot-welding process. Of course, their customers may have demanded a material with no split, which would have forced the current direction through the cell-tip, rather than side-stepping through the bus itself.
I do believe it is possible for the cladding process to make bus material cheaper than electro-plating. They also mention that the symmetry of the clad materials helps it retain its shape when it heats up. If there were only two layers, the copper might expand from heat faster than the nickel, causing a pressure for the strip to bend. That being said, our goal is to allow a DIY battery pack that does not get hot when providing 15A-20A peaks per cell.
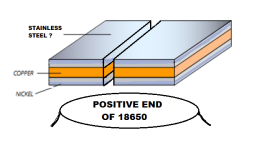
Is thin stainless cheaper than pure nickel and readily available locally in major cities? (doesn't need to be ordered). The lower layer would NEED to be nickel instead of stainless, because its conductivity is 23/3 better (7 times?) than stainless. If someone here got stuck with an order of nickel-plated steel ribbon (after they ordered pure nickel ribbon) then, the Ni-plated steel would likely be fine for the top cap...
I'm even now wondering if yellow brass would be acceptable for the lower layer. Its conductivity is less than copper (so it is more weldable with existing DIY machines), but conducts better than nickel...28/100, compared to 23/100... Brass is soft enough to be cut by scissors, and it is cheaper than Nickel.