themadhatter106
100 W

Disc side:
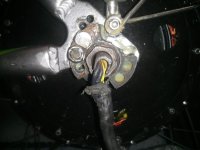
Chain Side:
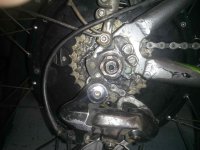
I need to completely redo both sides in a way which is stronger. I probably could have cut a little less off (maybe 1/8") in making room for the rack mount but that isn't a whole lot stronger.
What I really need are bolts on both sides of the torque arm. However, the holes in the torque arm are in the wrong place and too big of a hole on the other side to bolt down. I might be able to fill the hole with a weld. I think I want to make torque plates for both sides. I have an extra set of torque arms but I don't think that recutting them a bit closer would help that much. I can use my hydraulic press to push the old torque arm back together and then weld it down to some plate. I also really don't like having those big nuts sticking out on the derailleur side since it makes it much more difficult to tighten it with a wrench. I'd hate to drill more holes in my dropouts though. Any ideas?