CA V3 Simple Magura Curve Shaper
The CA V3 closed-loop throttle modes go long way toward refining throttle response, but there always seems to be a request for customizable throttle mapping. Throttle mapping is a more tractable problem with a V3 configured for current (or power) throttle since the mapping from throttle voltage to controller current is forced to be linear by the
CA PI control logic. Although active components or a tiny microprocessor are the usual vehicle for developing the throttle mapping curve, V3 configuration features make it possible to implement passive mapping circuits for resistive throttles like the Magura.
The image on the left below shows simple transfer functions that can be implemented with passive components. Unfortunately, the nature of such passive circuits leaves the output voltage ranges far out of alignment with the controller input range (typically 1v-4v). Although this classically has required active elements to perform scaling and level shifting, the V3 can be configured to accomplish these tasks. Assuming such configuration, the identical curves are redrawn on the right as a mapping of
percentage input to
percentage output - much more interesting...
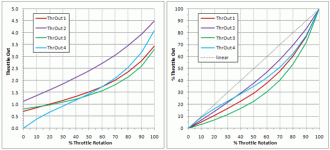
These curves were generated using this simple circuit:
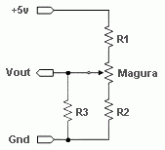
Manipulating the resistors has these effects (more or less):
- R1 is a current limiter used to hold the current to less than 5ma - the recommended V3 max draw for user circuits. Since this current must also power AUX Pot and PAS circuits, conservative power use may be important.
- R2 affects the slope of the curve at ZERO throttle. This is an indirect effect of sliding the throttle ZERO point up and down the transfer curve. Different portions of the curve will have different initial slopes.
- R3 controls the shape of the curve, lower values generally increasing the amount of curvature, higher values flattening the curve toward the unmodified linear transfer function.
As a side benefit, R1 also solves the
ThrI->FaultVolt issue with resistive throttles by ensuring that
ThrI->MaxInput is always less than 5v. For two extra resistors you get throttle shaping. See
this post.
- Note: This circuit is not well suited for use with trimpots because of the interactions of the resistances. If trimpots are used then fixed resistors should be added in series for R1 and R3 to ensure that the CA 5v regulator is protected from overload.
The Excel spreadsheet below is a simple designer tool to allow experimentation with various R values. The voltage ranges and maximum current are calculated and plots updated. This file was generated in Office 2007 and will work in 2003 although some of the colors may be remapped. It is operable in (free)
Apache Open Office although the colors are strange and the chart legends are incorrect.
The spread contains four sample designs that can be modified as desired. Here's a summary of the four samples:
View attachment 6
The samples appear on separate worksheets. Here are page images. Simply fill in values in the green cells and the tables and charts will update. The red lines show the actual input to output mapping - output voltage in terms of throttle rotation. The green line in the lower plot shows the output curve (red line) as a percentage of the unmapped linear throttle curve i.e. a comparison of mapped and unmapped outputs. For instance, in the example below, the mapped throttle starts out at about 95% of the unmapped throttle output, dips to 74%, then returns to 100%. (Maybe this curve might be useful for a lower powered DD that needs a little boost at the low end?)

The remaining three samples have increasingly large effect and are designed to illustrate only the range of adjustment - not desirability.
View attachment 4
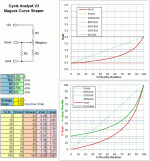
The shaper is easy to build as a M/F JST throttle adapter. The currents are tiny so power rating is not a consideration - 1/8W resistors were used below. The resistors in the completed adapter can be covered with a few drops of epoxy to bond the connectors into a solid unit.
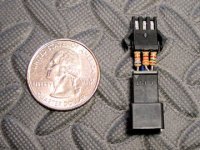
No promises as to the utility of this - either throttle mapping in general or the particular curves this circuit can yield - it seemed an interesting strategy worth putting out there. I personally prefer a 3-position switch to throttle mapping, but some mild mapping may find a way into my bike. I built circuits 2 and 4 above and both worked as expected. Unfortunately, freezing weather prevented all but a cursory test. Something conservative near circuits 1 or 2 might be beneficial for bikes with 3-position switches. Circuit 4 seemed better suited for bikes without speed switches - for instance, at 20% throttle the output is only 5% max. At 3.3kW, the low to mid-range tested pretty well, but the top end was a bit radical. As with any of these mapping 'solutions', you are stealing from Peter to pay Paul - for some part of the throttle curve to be more manageable, another part must suffer.
Anyhow - it's a simple circuit that only costs a few pennies to try - a nice side benefit of the V3.
