Hello everyone, i just placed an order on the "new" 75100 Pro V2 (apparently now the controller supports on/off switch and does not require an external anti spark switch thingy.)
Just wondering, has anyone already bought theirs and tested?
How is the performance, any overheating?
Any changes internally other than the on/off switch?
flipsky.net
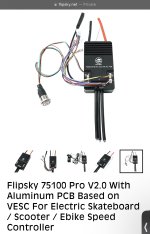
Just wondering, has anyone already bought theirs and tested?
How is the performance, any overheating?
Any changes internally other than the on/off switch?

Flipsky 75100 Pro V2.0 With Aluminum PCB Based on VESC For Electric Skateboard / Scooter / Ebike Speed Controller
Flipsky 75100 Pro V2.0 With Aluminum PCB Based on VESC For Electric Skateboard / Scooter / Ebike Speed Controller

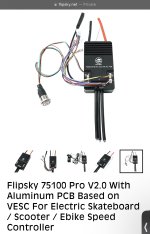