I have an adapter I'd like to make for CrazyBike2's jackshaft crankshaft, the one that receives the chains from both motor and pedals, to allow me to thread freewheels on it. This thread is essentially a call for resources and help to make one, and an explanation of why I want to use it, how it works, etc. I suspect others could use one too, if it already existed, but I haven't found one so far.
I once had something similar almost working, but it wasn't threaded on, I had to weld (into the threaded core of the freewheels) in washers I had filed the holes out square, to fit them onto a square-taper crankshaft, two of them side by side on the left side, so the motor and the pedals would not drive each other, and I could space the chainrings I attached to these freewheels farther apart than a simple triple chainring typically is, to prevent some of the problems it's been plagued with regarding chain derailing and tangling.
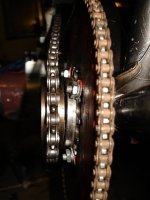
But nothing I could use to make those center-filler bits that I could still file would hold up for very long with even just the pedal forces at startup, and I sheared thru them quickly. Worse, welding onto the freewheels softened and destroyed the core piece, so the races and the pall bits broke away, so I wound up welding the freewheel inner and outer races together so I could continue using the bike, until I finally got fed up with fixing and remaking the cores with the filed-out holes, and just ended up using a regular bike triple (double sometimes) chainring there.
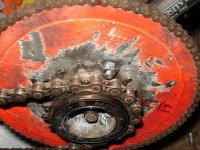
I designed an adapter even before I tried out the above, but don't have a way to make it. I can probably machine aluminum to the right size and shape, maybe, on my lathe, but I can't accurately make the hole for the square taper crankshaft, nor can I thread the inside and outside of it.

I might be able to drill and carefully file out the square taper hole, but I am not sure I can do it well enough to keep it all centered and balanced, unless I *start* with doing that hole first, then cut a sacrificial crankshaft (which I don't really have to spare) so I can chuck it up in the lathe, tamp down the unit on, and lathe away until it's cylindrically lined up with the square taper hole, and the right diameter to then be threaded outside. However, I then can't get it *off* the square taper shaft unless I have also first drilled out the hole on the other end, and tapped it's threads so I can use a crank puller on it. I don't have a way to tap these threads, and all the taps/dies I have found for these sizes are very expensive (usually at least $50 each, not including shipping, and I would need two sizes).
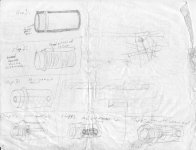
It doesn't have to be made with the outer lip, as I can probably use a pair of the lockrings off of crankshaft bearing races, plus spacer rings, to keep the freewheels from coming unthreaded.
It also probably doesn't have to be as long as it seems in the pic; I never determined if there is a "good enough" length for it, but I wanted it to be wider than just two freewheels, so I could space them as needed along there with shim washers between them to get whatever alignment with the pedals and motor I need (since obviously that isn't working out very well the way I have been doing it so far). Right now I am guesstimating 3" long.
Preferentially, I would like to get two of those oddball one-long-side crankshafts like the Cyclone kits have, to put one on this jackshaft to hold this device, and one on the pedals to make the chainrings on them stick out farther from the frame (there is a clearance problem with the batteries right now, preventing me from putting a side cover on there, among other things).
It also should be long enough so that I can optionally attempt to use a regular freewheel cassette of at least a few speeds, on the inside end (right) of it, in addition to the pedal freewheel. That way I can even have the motor shift gears separately if I wanted to--something that would require a completely independent jackshaft right now. It probably won't work very well due to the alignment problems I've had before, but it has not been something I could ever try, yet. It'd also require a smaller chainring on the motor output shaft than I currently have.
I once had something similar almost working, but it wasn't threaded on, I had to weld (into the threaded core of the freewheels) in washers I had filed the holes out square, to fit them onto a square-taper crankshaft, two of them side by side on the left side, so the motor and the pedals would not drive each other, and I could space the chainrings I attached to these freewheels farther apart than a simple triple chainring typically is, to prevent some of the problems it's been plagued with regarding chain derailing and tangling.
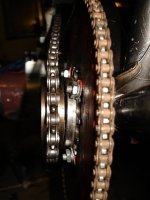
But nothing I could use to make those center-filler bits that I could still file would hold up for very long with even just the pedal forces at startup, and I sheared thru them quickly. Worse, welding onto the freewheels softened and destroyed the core piece, so the races and the pall bits broke away, so I wound up welding the freewheel inner and outer races together so I could continue using the bike, until I finally got fed up with fixing and remaking the cores with the filed-out holes, and just ended up using a regular bike triple (double sometimes) chainring there.
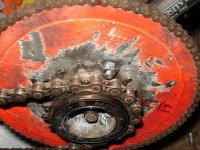
I designed an adapter even before I tried out the above, but don't have a way to make it. I can probably machine aluminum to the right size and shape, maybe, on my lathe, but I can't accurately make the hole for the square taper crankshaft, nor can I thread the inside and outside of it.

I might be able to drill and carefully file out the square taper hole, but I am not sure I can do it well enough to keep it all centered and balanced, unless I *start* with doing that hole first, then cut a sacrificial crankshaft (which I don't really have to spare) so I can chuck it up in the lathe, tamp down the unit on, and lathe away until it's cylindrically lined up with the square taper hole, and the right diameter to then be threaded outside. However, I then can't get it *off* the square taper shaft unless I have also first drilled out the hole on the other end, and tapped it's threads so I can use a crank puller on it. I don't have a way to tap these threads, and all the taps/dies I have found for these sizes are very expensive (usually at least $50 each, not including shipping, and I would need two sizes).
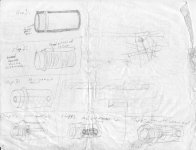
It doesn't have to be made with the outer lip, as I can probably use a pair of the lockrings off of crankshaft bearing races, plus spacer rings, to keep the freewheels from coming unthreaded.
It also probably doesn't have to be as long as it seems in the pic; I never determined if there is a "good enough" length for it, but I wanted it to be wider than just two freewheels, so I could space them as needed along there with shim washers between them to get whatever alignment with the pedals and motor I need (since obviously that isn't working out very well the way I have been doing it so far). Right now I am guesstimating 3" long.
Preferentially, I would like to get two of those oddball one-long-side crankshafts like the Cyclone kits have, to put one on this jackshaft to hold this device, and one on the pedals to make the chainrings on them stick out farther from the frame (there is a clearance problem with the batteries right now, preventing me from putting a side cover on there, among other things).
It also should be long enough so that I can optionally attempt to use a regular freewheel cassette of at least a few speeds, on the inside end (right) of it, in addition to the pedal freewheel. That way I can even have the motor shift gears separately if I wanted to--something that would require a completely independent jackshaft right now. It probably won't work very well due to the alignment problems I've had before, but it has not been something I could ever try, yet. It'd also require a smaller chainring on the motor output shaft than I currently have.