StillDre
10 mW
I'm looking to make my first ebike. I've gotten my hands on a 2019 Commencal Meta, I'd like to make it a commuter in a really hilly area, I also want to take it on some trails so ground clearance maters to me. I want it to be a mid drive because being able to shift gears lets any motor I use in it run efficiently and it's also fun. I could maybe get a kit but I am not happy with the ground clearance with Bafang kits and the other kits I've been seeing don't seem to be as powerful as I want, the really nice CYC kits are out of my budget.
I am also looking for a challenge, I want to diy almost all of the powertrain if I can. My current ideawill have the motor running legnth wise along the bike and use a 10:1 wormdrive gearbox to attach it to a shaft that then has a one way freewheel sprocket on it to deliver power to the chain. I have access to a capable 3d printer and a capable CNC mill so I'll use that to adapt a front freewheel to my current chainring. I want to be able to use the motor and pedal independantly of eachother. One of my goals is to add the ebike setup to my current chainline. The green indicates the chainline I would make Is to use a left side drive outrunner that I'll do a two stage reduction on. The first reduction will be inside the bike frame and the second will be between the wheel and the first reduction. I would like to do a reduction with belts but the second stage might need to be a chain instead.
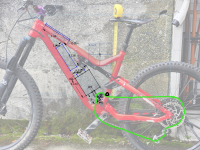
I was looking at using a QS90 80H and a Votol EM-50-4 which I can get for a little less than $300 but if I used that motor to it's full potential, it could probably tear the spokes out of my back wheel. The QS motor there could put out as much as 350nm at the sprocket if I geared it down to 100rpm. I need recommendations for physically smaller motors that can do over 100nm and 100ish RPM once geared down. That means that a motor that could put out 14000rpm and 1nm of torque would be a match. Outrunners and inrunners are fine, as long as it can sustain the torque. I'm also looking for cheap battery recommendations reasonably priced batteries that balance high current and capacity. I was planning on stacking SPIM08HP cells on the down tube and top tube for a 20s 1p setup but if I used 1p I would end up with a smaller capacity than I want and if I went with a 2p setup (the way they come stock from batteryhookup), I'd end up with a larger setup than I want, I could maybe do higher voltages with 1s but I'm worried about the voltages I can use on other motor/controller setups. I am also worried becasue those pouch cells are quite wide and may be hard to ride with. I am open to building the battery myself, it's a skill I've been wanting to build. The problem is that I can't find cheap cells that can do the current that I want without using a lot in parallel.
My budget is about 1000usd for the conversion but I'd rather spend less if I can.
Thank you anyone who had ideas or recommendations.
I am also looking for a challenge, I want to diy almost all of the powertrain if I can. My current idea
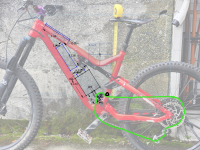
My budget is about 1000usd for the conversion but I'd rather spend less if I can.
Thank you anyone who had ideas or recommendations.
Last edited: