DingusMcGee
100 kW
After taking some measures to eliminate the likely hood of another chain jam occurring from the underside I got the most unusual chain jam. I was riding drifts of crusty snow higher than the bottom bracket on levelish ground when this chain looping event happened. No doubt, the crusty deep snow can push the chain upwards except maybe with the tightest of chains when using the big chain ring in the front and the big cassette on the freewheel. I was not in the tightest chain gearing configuration when the looping happened. You can also get underside jamming from chain bounce.
I have tried several obstruction plates & mechanisms to prevent the chain from getting in the space between the lower stays and the chain ring space [LSCRS] coming from the underside. The Lightning Rod mi-drive design using the 219 kart chain is notorius [I own one] for such chain jams and this is because the chain has pins that protrude beyond the flat plates of the chain. So the protruding pins of the chain can grab the a smooth 10 speed chain and push it into the lower stay-chain ring space [LSCRS]. But I was using the OEM 1/2 x1/8 BMX chain on the C-3000 with a half link. After adjusting the long pin on half link BMX chain to protrude outward as opposed to inwards I figured my stop gap mechanism would be successful. But I still was getting the most unusual JAM.
My first mechanism to prevent chain jams at LSCRS was to attach a plate on the outside of the stay facing the chain ring with enough thickness to leave about zero clearance between the chain ring and the stays. I am sure this worked some of the time but not enough of the time. Reason: The 219 chain with the protruding -- grabbing pins held the the rear chain good enough that it could be forced through this zero clearance space because the motor drive chain ring was deflecting outward during the squeeze through process of getting the chain into the LSCRS. This same jamming process may have been happening with the C-3000 due to that one protruding pin of the half link?
View attachment 8
The first attempt at a stopping mechanism is shown:
View attachment 7
Here is a similar plate is on the LRSB:
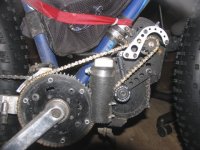
Because of chain ring deflection this side plate adaption did not work enough of the time to prevent the chain from ever getting into the LSCRS. Here is the current version of such a mechanisms that seems to be successful for the hardtail fat bike equipped with the LRSB.
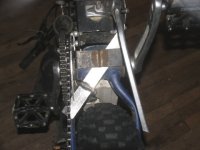
Another view of the normal plate:
View attachment 4
So far this normal plate is working but with enough motor BB chain ring deflection a large enough gap would allow the chain access to the LSCRS. It is that 219 kart chain with the protruding pins that grabs very effectively.
As for the full suspension bike with the C-3000 the same cross frame/stays normal plate as used on the hardtail fatbike was not fit-able. So a different plate fitting using channel aluminum was made that clamped on the underside of the stays:
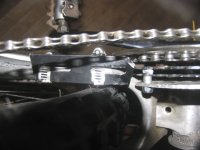
To further close the stop gap space a cross bolt spacer/blocker was added to the annular ring which is used to prevent inward falling of the chain near the stay.
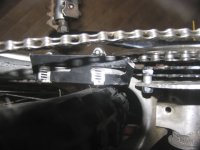
Even this closeoff of space was not fully adequate as there is a gap between the bolt and the small chaining. But even with not much space, still the unexpected can happen? Here is a view of the little bit of space between the cross bolt and the small chain ring.
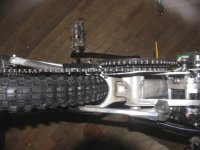
Recall the unusual chain looping event I mentioned at the start of this post? Here is what was happening in this little bit of space: Probably because I was running a narrow wide chain ring on the small ring the slackish chain had some tendency to stay attached/touching the lower side of the chaining. This effect and the effect of snow pushing the chain upward results in such a condition to fit and push the chain into the small space between the cross-bolt and the chain ring. One would think the pull of the chain would readily pull it out of this space but that did not happen as the scale of the space was such that once the chain was pushed through the gap, it took a configuration that with gravity kept it in such a loop. Oddly the chain would flow as if it were on a small pulley in this location. It would stay there with all throttle action and make plenty of noise -- never jamming. After getting the chain out it soon was pushed by snow into this configuration again. I then shifted gears to the chain ring set-up giving the tightest chain and it did not happen anymore. But I do not always want this gearing so I needed one more fix to get the chain blocker working.
Here we see the fix:
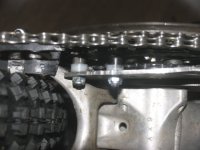
So much for solving detective like mysteries but so far there is no commercial device to stop gap such chain forcing events which can happen when riding in deep crusty snow.
There is another easy fix:
Run a tight chain and a one speed gearing.
I have tried several obstruction plates & mechanisms to prevent the chain from getting in the space between the lower stays and the chain ring space [LSCRS] coming from the underside. The Lightning Rod mi-drive design using the 219 kart chain is notorius [I own one] for such chain jams and this is because the chain has pins that protrude beyond the flat plates of the chain. So the protruding pins of the chain can grab the a smooth 10 speed chain and push it into the lower stay-chain ring space [LSCRS]. But I was using the OEM 1/2 x1/8 BMX chain on the C-3000 with a half link. After adjusting the long pin on half link BMX chain to protrude outward as opposed to inwards I figured my stop gap mechanism would be successful. But I still was getting the most unusual JAM.
My first mechanism to prevent chain jams at LSCRS was to attach a plate on the outside of the stay facing the chain ring with enough thickness to leave about zero clearance between the chain ring and the stays. I am sure this worked some of the time but not enough of the time. Reason: The 219 chain with the protruding -- grabbing pins held the the rear chain good enough that it could be forced through this zero clearance space because the motor drive chain ring was deflecting outward during the squeeze through process of getting the chain into the LSCRS. This same jamming process may have been happening with the C-3000 due to that one protruding pin of the half link?
View attachment 8
The first attempt at a stopping mechanism is shown:
View attachment 7
Here is a similar plate is on the LRSB:
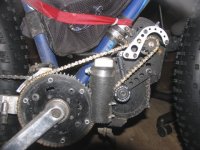
Because of chain ring deflection this side plate adaption did not work enough of the time to prevent the chain from ever getting into the LSCRS. Here is the current version of such a mechanisms that seems to be successful for the hardtail fat bike equipped with the LRSB.
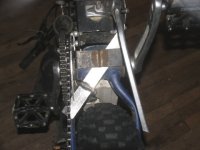
Another view of the normal plate:
View attachment 4
So far this normal plate is working but with enough motor BB chain ring deflection a large enough gap would allow the chain access to the LSCRS. It is that 219 kart chain with the protruding pins that grabs very effectively.
As for the full suspension bike with the C-3000 the same cross frame/stays normal plate as used on the hardtail fatbike was not fit-able. So a different plate fitting using channel aluminum was made that clamped on the underside of the stays:
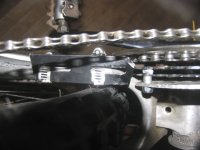
To further close the stop gap space a cross bolt spacer/blocker was added to the annular ring which is used to prevent inward falling of the chain near the stay.
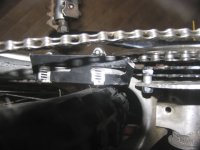
Even this closeoff of space was not fully adequate as there is a gap between the bolt and the small chaining. But even with not much space, still the unexpected can happen? Here is a view of the little bit of space between the cross bolt and the small chain ring.
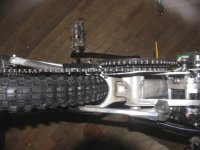
Recall the unusual chain looping event I mentioned at the start of this post? Here is what was happening in this little bit of space: Probably because I was running a narrow wide chain ring on the small ring the slackish chain had some tendency to stay attached/touching the lower side of the chaining. This effect and the effect of snow pushing the chain upward results in such a condition to fit and push the chain into the small space between the cross-bolt and the chain ring. One would think the pull of the chain would readily pull it out of this space but that did not happen as the scale of the space was such that once the chain was pushed through the gap, it took a configuration that with gravity kept it in such a loop. Oddly the chain would flow as if it were on a small pulley in this location. It would stay there with all throttle action and make plenty of noise -- never jamming. After getting the chain out it soon was pushed by snow into this configuration again. I then shifted gears to the chain ring set-up giving the tightest chain and it did not happen anymore. But I do not always want this gearing so I needed one more fix to get the chain blocker working.
Here we see the fix:
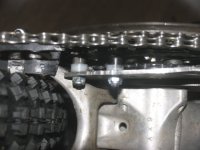
So much for solving detective like mysteries but so far there is no commercial device to stop gap such chain forcing events which can happen when riding in deep crusty snow.
There is another easy fix:
Run a tight chain and a one speed gearing.