I want an external balancer that can do all three battery technologies I am running.
Lion , LIFE and LTO.
I want an external balancer I can just plug in to any of those packs when needed and will balance in minutes , not hours.
Unfortunately only 6S , 7S and 8S external balancers exist and sometimes take hours to work. So a BMS or active balancer is the only options.
HOWEVER !!! If I could use one active balancer externally for all three battery types like an external 6S or 7S balancer and balance the pack when NOT running it then why does DA. think an active balancer is such a waste of money ?????
It is established that at least one of my LIFEPO4 packs have a low cell bank that seems to self discharge sometimes. It don't mean I have to tear the packs apart and re solder everything. That just seems absurd.
If I can attach the correct balance plug extensions into each pack : 6S , 10S LTO or 13S Lion then plug any of those packs that need balancing in that active balancer they should be balanced in a few minutes and ready to run.
Here is the active balancer I wish to convert to external balance via. the correct balance plugs from the different packs.
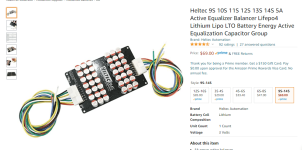
Notice the bottom pic where it says to weld those two terminals together for LTO. Will a plug or a switch work as I do not want to just balance LTO exclusively. I am sick of spending money so why I want to only buy one balancer instead of expensive BMSs for every pack.
This is e bike related and legitimate questions. My intentions are to solder a 13S balance plug to the 13S power modules. A 10S plug to each 10S - LTO pack and a balance plug to any other future packs and to my 6S LIFE packs if needed but probably wont need to as I have two 6S balancers as well as that 7S and two 6S LiPo chargers to deal with my 6S - LIFEPO4.
However an 18S LIPO4 spot welded in the future sometime seems like a great idea for the 3 kilowatt brushless controller so I can get full power or 3 kilowatts to the motor. Not sure if they sell an 18S balancer though. But could go with two 9S LIFEPO4 packs or spend a few extra bucks for an 18S external balancer if there is one.
Please let me know. LTO as well as active balancers is way over my head. Up until now I only dealt with 6S balancing when needed. But my BMSs failed. There is a good chance I could still save that 10S - 4P Laudation pack as I unwrapped it and can test cell banks and perhaps use that active balancer on it as well.
I did not drink last night and am up early. Thinking about going to the Home Depot for 1/4" plywood so I can start building custom boxes for the 13S power modules as well as two 10S - LTO packs.
Please let me know if I can use that balancer externally by soldering 10S and 13S balance plugs to the packs. Also I think it is Bluetooth so when I get up later as I am laying back down now I will search for 18S and Bluetooth as would be super cool to sit here on my laptop and see every cell balance or at least on my smart phone.
There is one.
https://www.aliexpress.com/i/1005001389756298.html?af=1424725&afref=&cv=47843&dp=826be8fc1d9af45000e41457849bd65c&mall_affr=pr3&utm_campaign=1424725&utm_content=47843&utm_medium=cpa&utm_source=admitad&aff_fcid=7cebfad6cae642dbb7ab504cb44da6b9-1631704878659-00630-_ePNSNV&aff_fsk=_ePNSNV&aff_platform=portals-tool&sk=_ePNSNV&aff_trace_key=7cebfad6cae642dbb7ab504cb44da6b9-1631704878659-00630-_ePNSNV&terminal_id=9581d40076cb4e08aa1132a6f5058123
Did not see the Bluetooth though. I want that.
https://www.aliexpress.com/item/1005003125644284.html
I like that one above way better than the others. It is fully enclosed like a regular 6 or 7S external balancer and don't have two different plugs which is confusing. It should work better as an external balancer like I want. It is worth the extra $$$$$.
https://www.aliexpress.com/item/1005003104573871.html?spm=a2g0o.detail.0.0.2cf9175c7M0RcL&gps-id=pcDetailBottomMoreThisSeller&scm=1007.13339.169870.0&scm_id=1007.13339.169870.0&scm-url=1007.13339.169870.0&pvid=0e549d6c-3ba0-4058-8630-51c21ff2b6bc&_t=gps-id

cDetailBottomMoreThisSeller,scm-url:1007.13339.169870.0,pvid:0e549d6c-3ba0-4058-8630-51c21ff2b6bc,tpp_buckets:668%232846%238112%231997&&pdp_ext_f=%7B"sceneId":"3339","sku_id":"12000024110134304"%7D
That one is cheaper. I need to do more research but at least you all know what I am looking to do and why.
I think DA said ""One BMS to rule them all" for the power modules.
I want one balancer to rule them all. Each and every pack that I own.
Please let me know.
Thanks.
LC. out.