casainho
10 GW
- Joined
- Feb 14, 2011
- Messages
- 6,058
So, I am developing and testing on a bad quality dual suspension bike. I could not found a good way to place the motor and at start I just let it rotate against the bike frame... and after some testing, it cracked as seen on the picture -- please be warned. Now, I put a metal clamp... you can see this can't work for bike that I will ride.
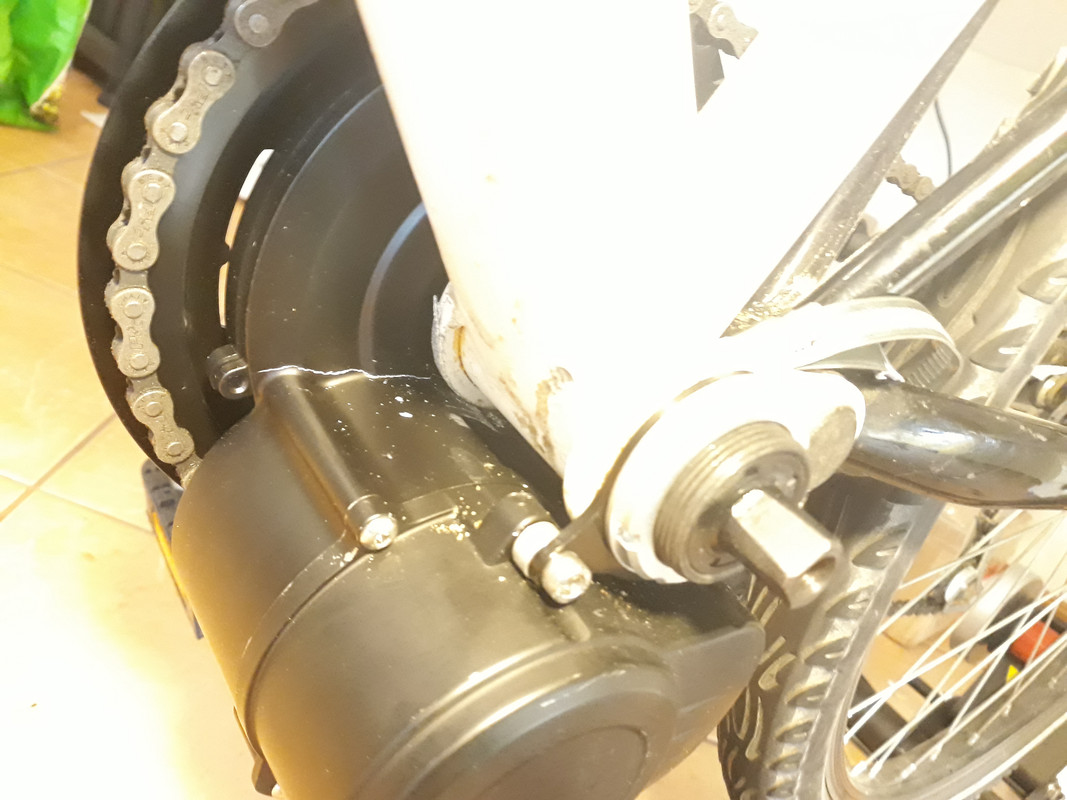
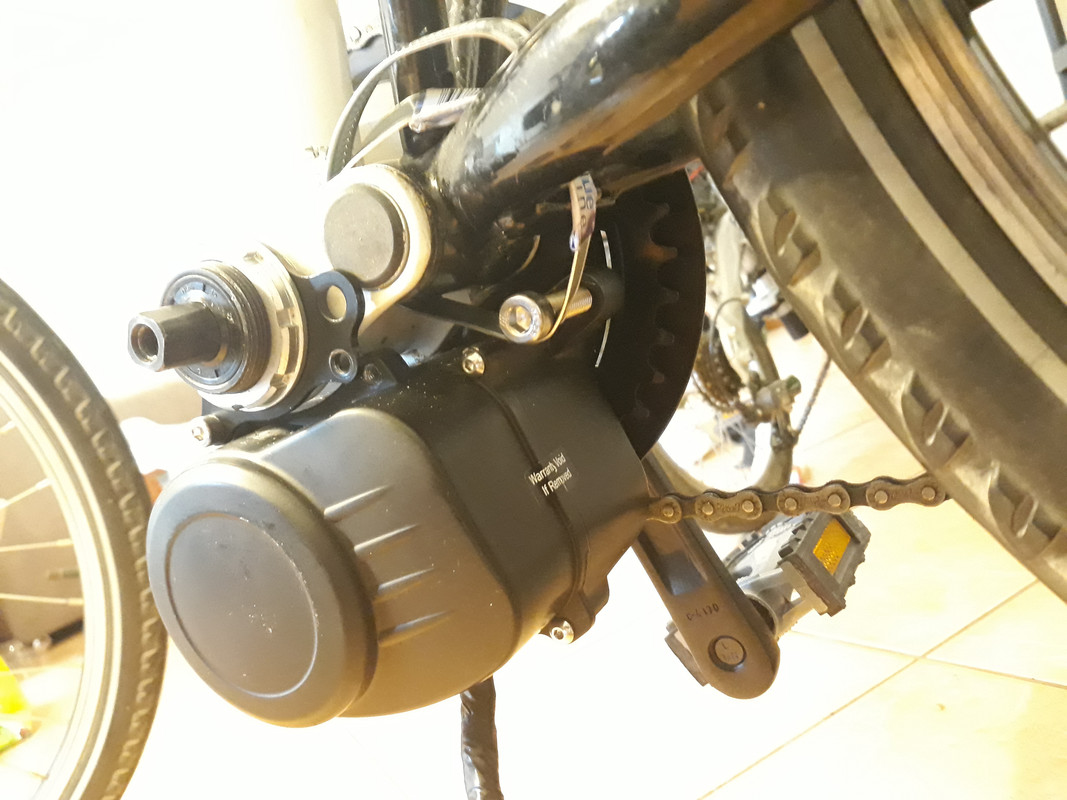
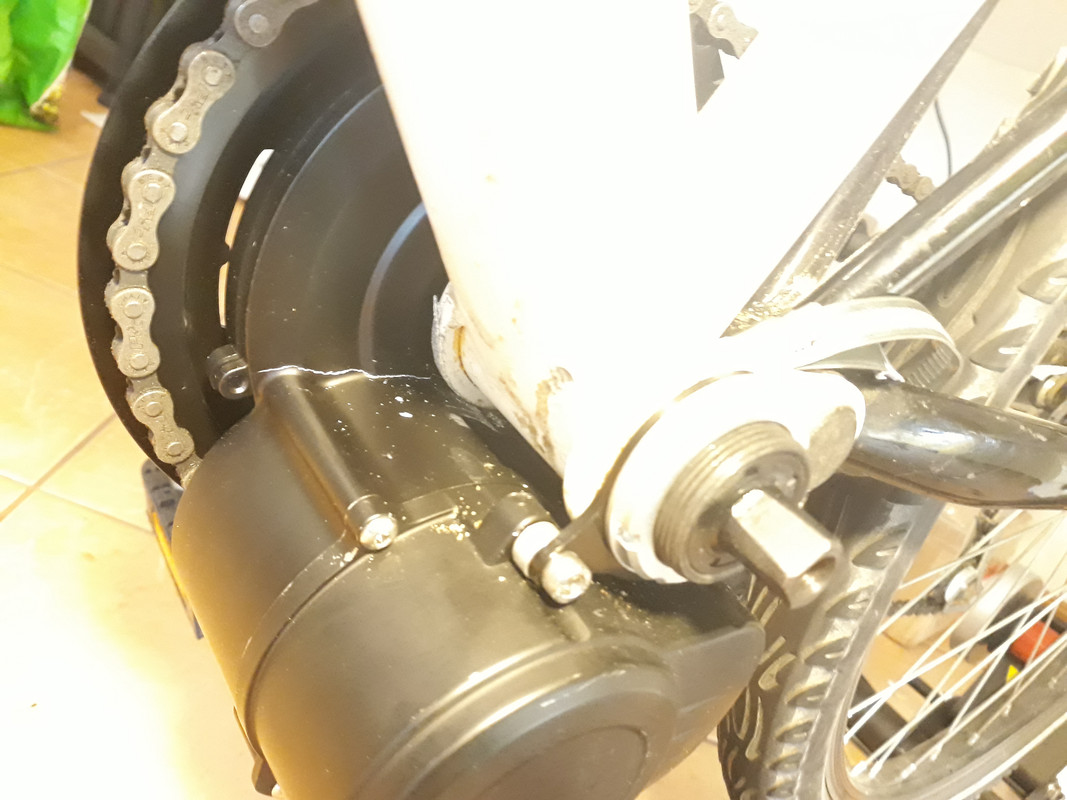
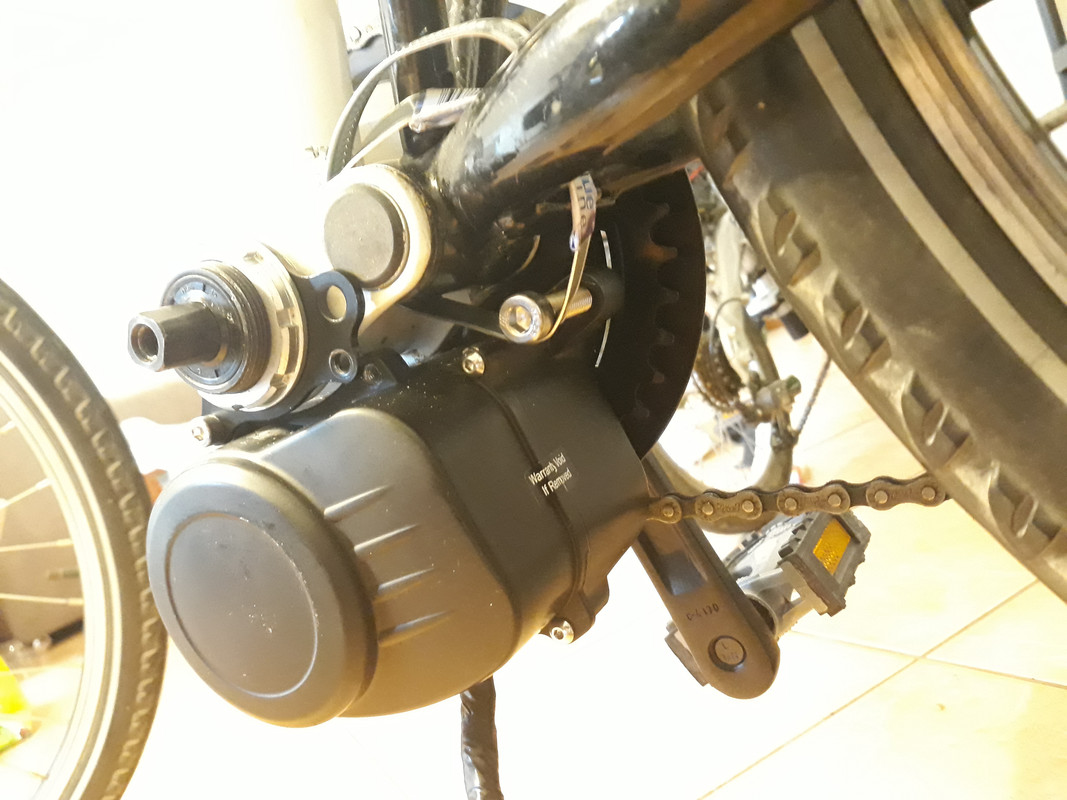