jbalat said:
Waynemarlow said:
Guys, I'm not sure what the problem is with the motor moving, if its fully located on the crank side of the BB and the non crank side plate is correctly installed ( yes you may well have to shim it with spacers to get the bolts correctly torqued ) and the large nut is correctly torqued,
Its hard with full suspension bikes because you are only relying on friction to hold it. If you do off road then the locking nut can come loose. Having a torque arm makes sense.
The stock motor attachment reacts torque with the torque arm. The "securing plate"
is not about transmitting torque. It gives a load path for up / down forces on the motor. Without the securing plate a force on the motor housing puts the casting is bending in a way likely to break it like you see in this photo
https://endless-sphere.com/forums/viewtopic.php?f=28&t=79788&start=2775#p1395963
Reacting the torque in friction is not what the design relies on. That is solid engineering practice. Friction is hard to estimate, surface contamination is a factor, torques are hard to ensure and even if a torque wrench is used the preload is not accurately know, etc.
But I can see why people with rear suspensions like the idea of using friction. They don't have a place to install the torque reacting plate. So I ran a few calculations to see how feasible it is. Assumptions:
0.2 coefficient of friction
Torque to react 80 N-m
Bottom bracket effective radius 19mm
No factor of safety
Two friction surfaces (both sides of the bottom bracket)
Pre-load you need from the M33.5 locknut: 10,526N (2366 lb).
To get there you need to apply 66N-m torque (49 ft-lb), but that is not an accurate calculation because differences in thread friction throw it off. I would at least double the torque applied and closely watch to see if it slips. Can the wrench that comes with the unit apply 135N-m (100 ft-lb)? Maybe. It is probably best to extend it. If you extend it and apply 100lbs at 1 foot you are close. Maybe maybe not. That is definitely more preload than an engineer would expect from that wrench. Would it hurt the TDSZ2? Would the preload hurt the TDSZ2? I can't tell for sure. There is an inside radius on the casting that would see more stress.
I like the serrations Bafang puts in their unit. Serrations work, how well they work requires close analysis. If I had rear suspension bike I would try this Nord-Lock serrated washer if you have enough threads showing. It is big enough. It is cheap. Maybe it would work if torqued highly, say 100 ft-lb.
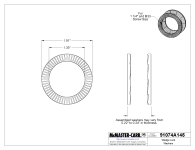