speedmd
10 MW
The bicycle disk trend is moving toward a large center hub mounted type rotor. Lots of options for mounting around the outside of a huge bearing.


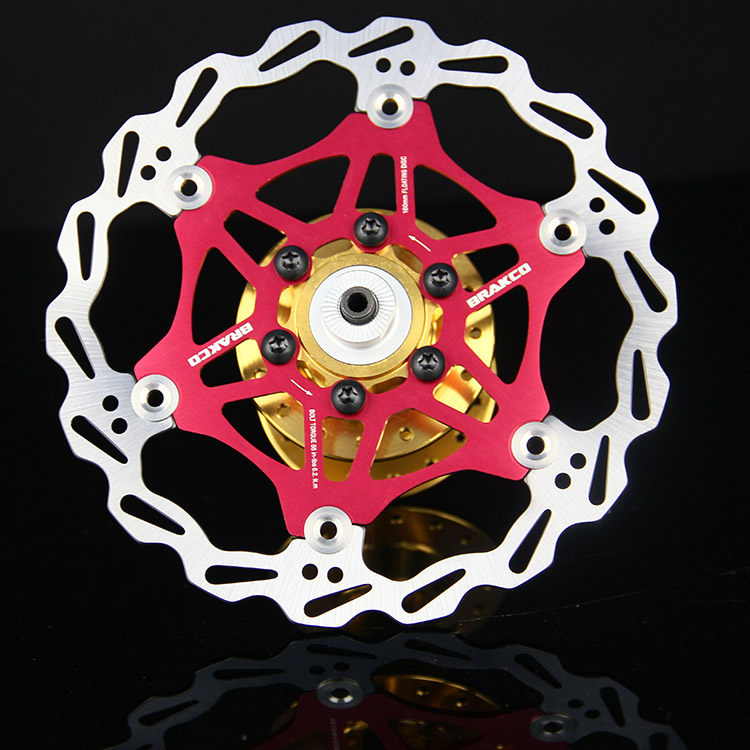
speedmd said:One thing to consider is the twofer you can get with such a left side heat sink/ cooling concentration as it could vented/ducted in a way to help cool the rotor also.
Indeed you hit the nail on the head there Justin...a few of the many reasons I gave this a go to begin with. I don't have many tools, or cash to throw at fancy setups, but simple cheap fans I can do.justin_le said:Ah sorry, I thought I saw some posts to the effect of just purely internal fans without additional vent holes but may have construed that in my mind from reading too quick! At low to moderate RPM's there's no doubt that would be a big boost over trying to passively encourage air flow through holes in the plates from just the motor rotation. Previously I was put-off by the idea of active powered fans in the hub before as being inelegant, but that's a bit of prejudice. In practice this seems like a very sensible and inexpensive approach, and as you say remains equally effective at super low speeds which is often the case when hub motors are at their maximum load on those long steep hill climbs.
madin88 said:i have some questions:
i would like to see the fins you installed inside the MXUScould you post a pic?
did you only painted the sidecovers or the entire inside incl stator, windings and magnets?
you have tested one MXUS with black paint and another with fins, right? not one with both mods?
during the high power tests you have pushed to core to 100°C, what was the temperature during the low power test?
I would like to do some calculations, but i'm not totally sure if i interpret the graphs right. could you please help me or tell me if i do it correct?
Ok, the vertical line shows conductivity in watts/°F between stator and shell and the horizontal line shows how much influence the rpm have.
During the high power tests the stator has 100°C and shell stays at maximum 65°C in steady air, so the delta T is 35°C.
now the math for MXUS at 300rpm (without mods):
Cowardlyduck said:I'm still yet to do proper, graphed testing, but today just did a quick test in the backyard.
http://endless-sphere.com/forums/viewtopic.php?f=30&t=56965&p=1072763#p1072763
The rate the temp drops when the fans are running shows pretty clearly how effective they are.![]()
kd8cgo said:Lol yeah, the axle would remain steel, but the main design change is to move the bearing from a small one on the axle to a much, much larger one that allows for an aluminum heat sink to poke through, around the axle. The outer surface of that aluminum heat sink would then be where the bearing/bearing race would be installed. That was the point of the brake rotor with a larger internal bolt circle - so it can mount to a motor side plate that effectively has a a giant 3-4" hole in it. All of this is possible just by solving/making a cost effective large bearing assembly on that side.
edit: The primary advantage of the large bearing allows a large, short path for thermal conduction from the stator winding region to the "outside world" - it removes the inherent limitations of having a multi-step radiant heat path to follow.
justin_le said:This would also work brilliantly well with an all-internal heat pipe to move things from the stator to a finned heatsink protruding from the insides of the large ID axle. Kinda makes a lot more sense than trying to run heatpipe tubes right out of the motor to a fork mounted heatsink. And it's much less weight to run a few heatpipe tubes inside the motor than to have sufficient metal mass to move similar heat volumes via conduction.
kd8cgo said:I'm wondering how much extra mass would be needed for sufficient convection, say if the stator carrier is made of aluminum instead of steel.
If the two are modeled, then a side by side cost comparison can be made. I have no idea how much heat pipes cost, I imagine they are not that expensive. Of course I have no idea the costs at manufacturing scale for aluminum or heat pipes. I figure if relatively giant aluminum wheels for cars are less than half the price of an average consumer hub motor, it might not be too bad. I wouldn't be surprised if the steel displaced from a traditional hub motor design would make the non-phase change convection model less massive than first anticipated.
I take it these floating rotors don't have an ISO standard bolt pattern that could be cast into a hub side plate in order to toss the center hubs... I was afraid of that. Still might be a cool idea for the DIY crowd.
justin_le said:I think you mean conduction not convection,
justin_le said:I was a bit concerned about overall noise levels for when we move this into the lab upstairs and have it running for hours at a time waiting for motor shells to reach steady state temperatures. So we did a plot comparing the wind speed, fan RPM, motor power, and decibel level at 2 m away and the results look like this. Hit 70dB at 25 kph which is OK, but nearly 80dB at 50kph is noise cancelling headphone time:
macribs said:There are no debate if oil cooling is better or not, it is widely agreed upon the effectiveness of oil cooling a hub motor. In fact the fastest e-bike up Pikes Peak was using oil filled hub.